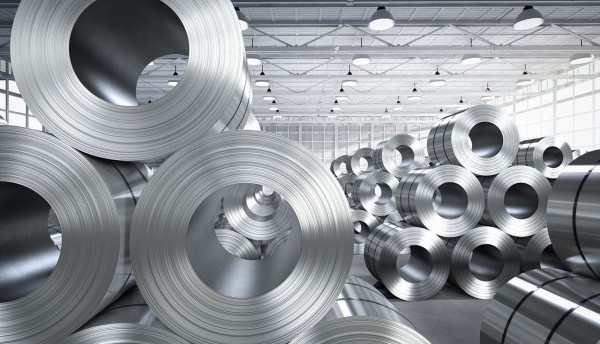
The automotive industry is increasingly focused on reducing vehicle weight to enhance fuel efficiency, reduce emissions, and comply with stringent regulations. Steel, a primary material in vehicle construction, plays a pivotal role in this lightweighting trend. The shift toward lighter vehicles is driven by regulatory frameworks such as the EU's CO2 emissions targets, which mandate a reduction in average fleet emissions to 93.6 g/km by 2025, and the UK's zero-emissions vehicle (ZEV) mandate, which requires a growing proportion of electric vehicles in manufacturers' offerings.
To meet these regulations, manufacturers are adopting advanced high-strength steels (AHSS) that provide superior strength-to-weight ratios. These steels allow for thinner components without compromising safety or performance, effectively reducing overall vehicle weight. Lightweighting is particularly crucial for EVs, where battery weight typically adds around 0.5 metric tons. By minimizing the weight of the vehicle's body structure, manufacturers can improve the range and efficiency of EVs, which is essential as the automotive sector transitions towards electrification.
Sustainability is another critical consideration in the use of steel for lightweighting. Life cycle assessment (LCA) methodologies help manufacturers evaluate the environmental impact of materials throughout their life cycle. A cradle-to-grave approach emphasizes the importance of end-of-life recyclability, particularly for steel, which boasts recycling rates exceeding 90%. However, the production processes also matter; steel produced via electric arc furnace (EAF) technology has a significantly lower carbon footprint compared with traditional blast furnace methods. This shift is vital in addressing the carbon emissions associated with steel manufacturing, especially in light of the EU's carbon border adjustment mechanism (CBAM) that targets high-emission industries.
Tata Steel is at the forefront of addressing lightweighting challenges by committing to EAF production by 2028, which will enable the production of AHSS with a 50% lower CO2 footprint than conventional methods. This transition not only aligns with regulatory requirements but also supports the automotive industry's sustainability goals. Tata Steel is also focusing on enhancing the quality of recycled steel and improving separation techniques to ensure high-quality raw materials for future production. By prioritizing lightweighting and sustainability, Tata Steel is positioning itself as a key partner for automotive manufacturers navigating the complexities of modern vehicle design and regulatory compliance.
To learn more, we spoke to Market & Business Development manager, Sustainability at Tata Steel UK, Nick Silk, and Head of Customer Technical Services at Tata Steel UK, Kevin Edgar.
Key takeaways:
- OEMs must now prioritize sustainability in their designs due to strict EU and UK regulations aimed at reducing emissions and promoting EVs. While there is a regulatory push for EV adoption, consumer demand is hindered by cost and infrastructure challenges. Additionally, the upcoming carbon border adjustment mechanism (CBAM) will encourage OEMs to use lower-carbon materials, particularly in steel production, to meet sustainability goals and manage costs effectively.
- Lightweighting remains crucial for meeting fuel economy and emissions regulations, especially for hybrid and electric vehicles, as reducing vehicle weight enhances efficiency and range.
- Adopting a cradle-to-grave approach in life cycle assessment helps manufacturers evaluate the full environmental impact of materials, emphasizing the need for recyclability at the end of a vehicle's life, particularly for steel.
- Tata Steel is transitioning to EAF production by 2028 to produce advanced high-strength steels with a significantly lower carbon footprint, supporting the automotive industry's lightweighting goals.
- Utilizing recycled steel can substantially reduce the carbon footprint of electric vehicles, with 50% recycled content potentially decreasing emissions by up to 0.8 metric tons CO2, highlighting the importance of effective recycling processes.
Nick Silk
Kevin Edgar
The following is an edited transcript of the conversation.
S&P Global Mobility: How do you see regulatory changes and consumer demand for sustainability influencing the adoption of lightweight materials in the automotive industry?
Tata Steel: OEMs have traditionally balanced cost, weight, and performance when designing vehicles. Now they are balancing cost, weight, performance, and sustainability.
There are various EU and UK regulatory changes shaping carmakers’ sustainability goals.
In both the EU and UK, legislation is in place to reduce vehicle tailpipe emissions and increase the number of electric vehicles that OEMs sell. In the EU, automakers need to comply with emissions targets or face heavy fines. In 2025, the fleet average target will tighten from the current 116g/km CO2 limit to 93.6 g/km CO2. In the UK, the Zero Emissions Vehicle (ZEV) mandate compels manufacturers to sell an increasing proportion of electric vehicles, starting this year (2024) at 22% and rising to 80% by 2030.
Currently, there is very much a regulatory push for electric vehicles (EV) over a consumer pull. The cost of migration to EV (by consumers), both upfront costs and charging costs, means that many people won’t make the switch because it costs more than the equivalent ICE. People might want to be more sustainable but cannot afford it at the moment. Additionally, there are other barriers to EV adoption, such as charging infrastructure and range anxiety. Low embodied CO2 vehicles are not currently a consumer issue. We experience the demand for more sustainable products coming from regulation and from the automotive manufacturers themselves who are setting their own targets to meet or exceed regulatory requirements on the carbon footprint of materials and recycled content levels, for example.
Draft EU recycled content legislation will likely set a minimum recycled content for products sold in Europe from 2030, and this is driving OEMs to establish internal goals on recycled content by material.
Finally, the carbon border adjustment mechanism (CBAM) is being introduced to tax CO2 emissions for high-emitting industries like steel manufacturing in the EU and UK in similar but separate schemes. CBAM is intended to provide a level playing field by applying a border tariff on imports that do not incur an equivalent cost of emitting CO2. Emitting CO2 in steel production in the EU and UK will also be taxed more heavily. CBAM will be introduced from 2026 in Europe and 2027 in the UK.
The purpose is to ensure that the cost of carbon is realized whatever the carbon footprint of the steel and whatever its country of origin. CBAM is therefore driving steel manufacturers to reduce the carbon footprint of their products, and this financial incentive is likely to drive OEMs to prioritize lower-carbon steel alternatives. By opting for steel that incurs fewer carbon emissions, OEMs can mitigate costs associated with the CBAM and enhance their sustainability profiles.
What role does lightweighting play in meeting regulatory requirements for fuel economy and emissions?
The drive to adopt lightweighting materials has certainly not decreased as a result of regulatory-driven electrification. For hybrid vehicles, the second drivetrain and battery add to the vehicle weight, and in the case of a full EV, the battery weight is typically 0.5 tonnes [metric tons]. Vehicle weight affects the range and efficiency (kWh/km) of EVs and the mpg of hybrid vehicles, so it remains very much the focus to minimize weight where possible using lightweighting materials.
Lightweighting, as a means to affect EV range, will remain for the car body structure whilst the cost of batteries is high, and motor performance is being developed. However, in the future, the benefit of body structure lightweighting will be surpassed by better-performing motors leading to lighter battery packs. Advances in this area will be far more beneficial in the long term. Affordability of weight saving is also key.
How does life cycle assessment (LCA) impact material choices in vehicle design for enhanced sustainability?
Life cycle assessment considers the carbon footprint of a product through the stages of its life cycle. A "cradle-to-gate" approach considers the production of steel from extraction of raw materials to the point the steel leaves the steelmaker’s gate. When automotive manufacturers take a cradle-to-gate approach, they observe the upfront embodied CO2 of a product — the CO2 emitted as a result of manufacturing the product from the input materials to the point it is supplied to the OEM. This highlights that products manufactured from raw materials via the blast furnace/basic oxygen steelmaking process have a substantially higher carbon footprint than products manufactured via the EAF [electric arc furnace] route with increased scrap input, putting significant pressure on steelmakers to reduce the carbon footprint of their processes and increase recycled content.
Taking a cradle-to-gate approach that focuses on upfront embodied CO2 can risk selecting fewer recyclable materials with lower upfront embodied CO2, so it is important that end-of-life recyclability is considered in materials selection.
In comparison, a "cradle-to-grave" approach considers the full life cycle to the point of recycling the product at end of life. This approach accounts for the recyclability of the vehicle at the end of life and therefore of its constituent materials. Steel is readily recovered from end-of-life vehicles and achieves recycling rates of >90%, so is seen favorably as a material of choice.
What environmental considerations are important regarding the production and end-of-life recyclability of lightweight materials?
Modern-day vehicles comprise a vast range of advanced materials, and the primary environmental consideration is the separation of these materials at end of life to ensure that each material type can flow back into its own circular production route. Separation and sorting of materials from end-of-life vehicles, therefore, has to be a primary focus.
In the case of steel specifically, the corrosion warranties that we are all now so used to with modern vehicles come from the use of zinc-coated steel. In the primary blast furnace BOS [basic oxygen steel] steelmaking process, zinc-coated steel is not readily recycled, but EAF steelmaking is ideally suited to processing zinc-coated steels. Furthermore, in the future, the zinc dust from our fume-extraction facilities will be sold directly to the zinc industry for recycling.
How does Tata Steel plan to support the automotive industry's lightweighting goals through green steel production?
The focus of lightweighting by the automotive industry is on the “body-in-white” — the structure of the vehicle that gives it strength and rigidity to meet safety requirements. This is where the advanced high-strength steels are found that give equivalent or enhanced performance for a reduction in weight.
EAF production is ideally suited to lightweighting and the production of high-strength and advanced high strength (AHSS) steels, as is readily demonstrated by a number of EAF-based US steel companies who routinely manufacture these products. Tata Steel UK has committed to transition to EAF steelmaking by 2028 and investment in secondary steelmaking technologies that are specifically designed to make these AHSS. This will lead to a focus on affordable body structure.
What sustainable practices are you implementing to improve the life cycle emissions profile of your steel products?
Core to our strategy, Tata Steel UK has committed to building an EAF, which will be operational by early 2028 and producing steels with typically 50% lower CO2 footprint than today. Once operational, we will progress schemes to further improve life cycle emissions, such as using renewable forms of carbon in our processes and working with suppliers to source lower carbon footprint inputs to our products. We have an ongoing program of electrifying our downstream processes and taking increasing advantage of sourcing renewable energy.
How do you ensure compliance with EU regulations on material circularity and recycling in your production processes?
The primary blast furnace, basic oxygen steelmaking process is limited to recycling about 20% of scrap due to constraints on energy input. The electric arc furnace process, on the other hand, is powered by vast quantities of electrical heat input and is entirely flexible in terms of the proportion of recycled content.
For the automotive sector, we will be able to offer products with 50-80% recycled content from the EAF furnace, which will comfortably ensure compliance with EU regulations and support OEMs in meeting their corporate circularity targets.
What challenges do manufacturers face when transitioning to advanced steel for lightweighting, and how can Tata Steel assist in overcoming these obstacles?
There are three main challenges: The inherently higher strength of advanced high strength steels, the potential difficulties in joining these steels to themselves and other steel types and sensitivity of cut edges to cracking.
Higher strength steels are inherently more difficult to form into complex shapes — requiring more force and resisting the forming operation — an issue known as "spring-back." The issue is well-known to OEMs, but Tata Steel can supply reliable data with which to model forming operations and inform press setup, as well as working in partnership to explore solutions modifying the part design and press settings.
The joining of advanced high strength steel — so-called weldability — and sensitivity of cut edges to cracking are both best addressed by Tata Steel at the design stage of the steel chemistry and how it is processed, but again Tata Steel offers practical support to customers concerning spot welding, material selection, etc.
How does the use of recycled steel contribute to reducing the carbon footprint of electric vehicles?
The World Steel Association uses the approximation that a one percent increase in recycled content reduces the carbon footprint of steel by 16 kg. At 50% recycled content, this equates to about 0.8 t [metric ton] CO2 reduction, and at 100% recycled content, to a 1.6 t [metric tons] CO2 reduction compared to current primary steelmaking methods. Given that steel typically contributes 0.5 to 1 tonne [metric ton] to the weight of a vehicle, recycled steel will offer at least a 0.5 t [metric ton] reduction in the carbon footprint of an electric vehicle and potentially up to 1.5 tonnes [metric tons] (carbon footprint reduction).
What innovations are Tata Steel pursuing to enhance the quality of recycled steel for high-performance vehicle components?
There are a couple of fundamentals that help with understanding how to best enhance the quality of recycled steel: (i) Ferrous scrap is steel that has had a previous life — it was designed with a specific purpose in mind, so recycling it into a steel for a similar purpose will always maximize its potential in re-use. (ii) Products often comprise a range of materials, and incomplete separation of steel from other metals (e.g., copper or aluminium) or from non-metals (e.g., plastics or glass) reduces the quality of recycled steel, but also, of course, inhibits the circularity of the non-ferrous/non-metallic components.
Tata Steel’s primary focus is to work with the supply chain to enhance separation and sorting of scrap to improve its quality via projects such as Rectifi: A collaboration between industry partners and research institutions, which focuses on enhancing the recycling and reuse of industrial scrap, particularly in the steel and metal sectors.