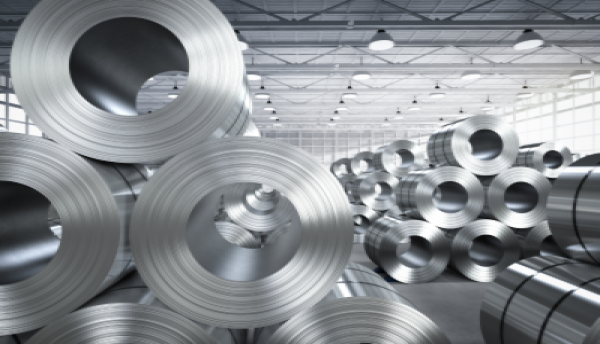
The automotive industry is increasingly adopting diverse materials to achieve lightweighting, crucial for enhancing fuel efficiency and reducing emissions. Traditional materials like steel are being complemented or replaced by advanced high-strength steels, aluminum, composites and magnesium.
Advanced high-strength steel (AHSS) allows for thinner sections without compromising strength, enabling manufacturers to reduce weight while maintaining safety and structural integrity. Aluminum, known for its lightweight properties, is extensively used in body panels and engine components, although its production is energy-intensive, raising sustainability concerns.
Composites, including carbon fiber and fiberglass, offer weight savings and design flexibility. These materials are beneficial in high-performance and electric vehicles, where reducing weight can enhance range and performance. However, challenges in cost and recyclability remain.
Magnesium is another lightweight alternative, often used in engine blocks and transmission cases, due to its excellent strength-to-weight ratio.
Despite the growing use of alternative materials, steel remains a cornerstone of automotive design. Its versatility, recyclability and cost-effectiveness make it an enduring choice. As the industry evolves, advanced steel technologies will continue to play a vital role in achieving lightweighting goals while ensuring sustainability.
To learn more, we spoke to Russ Balzer, technical director of World Auto Steel, an organization focused on advancing the use of steel in the automotive industry. It aims to promote the benefits of steel as a sustainable, cost-effective and versatile material for vehicle manufacturing. World Auto Steel also advocates for policies that recognize the environmental advantages of steel, such as its recyclability and life cycle sustainability, helping the automotive sector transition to more sustainable practices.
Key takeaways:
- By using a combination of different materials or varying grades of a single material, designers can enhance strength and durability where needed while minimizing material usage in less critical areas. This tailored approach not only contributes to overall vehicle lightweighting but also improves performance, fuel efficiency and sustainability, aligning with modern automotive design goals.
- Regulations now require manufacturers to consider the full life cycle impacts of materials, shifting focus from solely tailpipe emissions to a broader environmental perspective. As regulations like the EU’s Light Duty Vehicle CO2 standard evolve, they incentivize manufacturers to integrate life cycle assessments into their material selection processes.
- The production of lightweight materials, such as aluminum, composites and magnesium, often comes with significant environmental costs due to their energy-intensive manufacturing processes. Compared to steel, these materials can produce primary emissions that are six to seventeen times higher.
- By employing life cycle assessment (LCA), manufacturers can identify trade-offs and assess the net environmental effects of different materials, particularly when considering lightweight alternatives. This approach helps ensure that lightweighting strategies do not inadvertently lead to higher emissions in other phases of the vehicle's life.
The following is an edited transcript of the conversation.
S&P Global Mobility: When considering alternative materials in vehicle manufacture, what are the key considerations and challenges that need to be addressed?
Russ Balzer: While functional performance, manufacturability and cost all are important considerations for material selection in vehicle manufacture, sustainability has emerged as a critical element of that decision process.
Sustainability considerations include life cycle impact on the vehicle (does use of the alternative material result in a net positive environmental impact over the life of the vehicle?), recyclability (is the alternative material not only recyclable, but also actually recycled?), and circularity (can the alternative material be used in such a way as to promote the creation, retention, and recovery of value?).
How does the use of multimaterial design contribute to weight reduction in vehicles?
Using a variety of materials or different grades of a single material enables designers to optimize vehicles for lightweighting by more closely matching a material’s properties to a component's requirements.
For example, some components require higher strength and durability. Using higher-strength materials can enable the vehicle designer to make the sections thinner, thereby using less material and saving weight.
Steel’s current advanced high-strength steel portfolio contains 64 distinct grades, featuring a range of key properties, including strength, ductility, surface quality and bake-hardenability, for example. This allows designers the flexibility to use only as much material as they need to meet functional requirements.
How do you see the evolving regulatory landscape and consumer demand for sustainability influencing the adoption and use of lightweighting materials in the automotive industry?
The demand for more sustainable vehicles, from both a regulatory and a market perspective, drives a closer examination of the environmental advantages and disadvantages of materials, demonstrating that the traditional approach of focusing solely on tailpipe emissions can force vehicle manufacturers into lightweighting strategies that can be antithetical to their sustainability goals.
Increasingly, regulators and consumers recognize that a life cycle perspective is the optimal way to understand these impacts. A good example of this is the European Union’s latest Light Duty Vehicle CO2 Standard, which requires the development of a method that vehicle manufacturers can use to calculate and report the emissions of their vehicles on a life cycle basis. These types of regulatory shifts will provide an incentive for automakers to make material decisions with life cycle/sustainability as a key consideration.
What are the environmental considerations in the production and end-of-life recyclability of lightweight materials?
For production, considerations include the energy used to produce the material, and the environmental impact of generating that energy. Alternative materials used for lightweighting, like aluminium, composites and magnesium, are very energy-intensive to produce, and therefore come with higher production emissions as well. When compared to steel, all other automotive structural materials currently have primary production emissions, which are between six and 17 times higher.
For end-of-life recyclability, there are several key factors:
- To effectively reduce the need for virgin material production, recycled materials must have properties comparable to those of virgin materials. This ensures that the recycled material can perform the same functions without compromising quality.
- It is important to understand not only how recyclable a material is in theory, but also how much recycling is taking place in practice. Plastics are a good example of this: while the material is easy to recycle, only a small fraction of post-consumer plastic waste is actually recycled.
Compare this to steel, which is infinitely recyclable with no loss of properties, meaning recycled steel can be used for any application. In practice, because its magnetic properties make it easy to recover and there is a strong and well-established global steel recycling infrastructure, the global recycling rate for steel from automobiles is around 95%.
How does the concept of LCA influence the choice of materials in vehicle design?
LCA evaluates the environmental impact of a product across its entire lifecycle. Only by understanding the impact across the entire life cycle can vehicle manufacturers evaluate trade-offs and assess the net impact of the product they’re using.
A good example of this is the use of alternative materials in vehicle design — many used for lightweighting are energy-intensive (and therefore emissions-intensive) to produce. While these materials can have positive effects in other phases of the vehicle’s life that outweigh the additional impacts, this is not always the case. They can also result in unintended consequences, such as higher emissions. LCA is a critical tool in helping manufacturers strengthen the sustainability of their vehicle.
What role does lightweighting play in meeting regulatory requirements for fuel economy and emissions?
While lightweighting plays a well-understood role in meeting regulatory requirements for fuel economy, emissions is a different story. We understand, through life cycle assessment, that there are significant sources of emissions beyond just fuel. Therefore, it’s important to consider improvements in fuel economy and emissions reduction separately:
The connection between lightweighting and fuel economy is clear: Mass is a significant driver of tailpipe emissions. To achieve better fuel economy, vehicle lightweighting is an obvious choice, and because current emissions regulations are focused only on tailpipe emissions, better fuel economy means [lower] emissions.
However, a regulatory focus on only tailpipe emissions makes it impossible to measure and improve overall emissions by driving automotive manufacturers to make material choices that may not make sense from a life cycle perspective — choices that may result in overall higher emissions over the vehicle’s life and ultimately, cost consumers more money.
LCA bridges the gap between fuel economy and emissions. It is the only method to measure and regulate vehicle emissions that enables real, meaningful reductions.