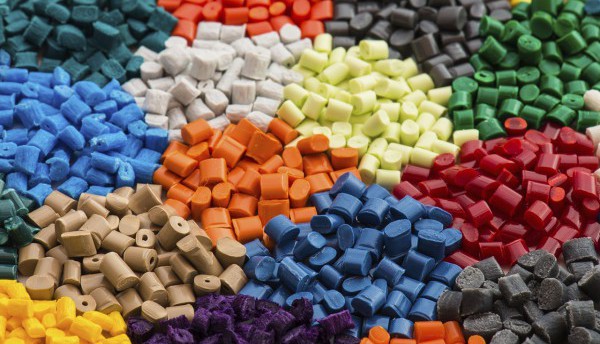
The automotive industry is increasingly turning to sustainable materials, particularly advanced polymers and composites, to achieve lightweighting and enhance vehicle efficiency. Lightweight vehicles contribute to fuel efficiency and reduce greenhouse gas emissions. Advanced polymers, such as bio-based plastics and thermoplastics, offer an eco-friendly alternative to traditional materials, while composites, which combine materials like carbon fiber with resins, provide strength without the weight.
Manufacturers are investing in research and development to create high-performance materials that not only meet safety and durability standards, but also minimize environmental impact. For instance, bio-based composites derived from renewable resources are being used in interior components, while lightweight polymers are finding applications in body panels and structural elements.
This shift not only supports regulatory compliance regarding emissions, but also aligns with consumer demand for greener vehicles.
To learn more, we spoke to executives of Envalior. Envalior specializes in sustainable materials, focusing on advanced polymers and composites that support circular economy practices. The company aims to reduce waste and enhance resource efficiency across various industries, including automotive and electronics. Envalior was formed in 2023 from the merger of two companies: the specialty materials business of DSM and the engineering materials business of Lanxess.
Key takeaways:
- The rise of electric vehicles increases overall vehicle weight due to additional components, affecting drivability and safety, which drives the need for lightweight composite materials.
- Composites offer a good balance of weight, stiffness and strength, making them suitable for modern vehicle designs, particularly in addressing noise, vibration and crash safety issues.
- Polymers and plastic-metal hybrids enhance design flexibility and performance, allowing for innovative shapes and reduced weight while maintaining necessary mechanical properties.
- New automotive applications for plastics are emerging, especially in electrification components, as modified polymers meet traditional metal requirements for thermal conductivity and flame retardance.
The following is an edited transcript of the conversation.
S&P Global Mobility: Can you explain how Envalior's Akulon Diablo material withstands high temperatures and contributes to weight reduction in under-the-hood applications in ICE vehicles?
Akulon Diablo exhibits exceptional high-temperature resistance while maintaining superior material properties. This allows for the use of plastics — offering benefits such as weight reduction, cost savings, design flexibility and enhanced sustainability — in high-temperature ICE applications where metal components would traditionally be required, thus overcoming metals' design limitations and weight constraints.
Can you share your observations on the current trends in lightweighting using composites in vehicle manufacture and how they impact overall vehicle performance?
The shift towards new energy propulsion in the automotive industry is accompanied by an increase in vehicle weight due to the additional components in electric vehicles, such as batteries. This added weight impacts vehicle drivability, increasing curb weight and reducing the stiffness-to-weight ratio, potentially leading to noise, vibration, and harshness issues. Additionally, in the event of a collision with a non-EV vehicle, the imbalance in crash weight could result in an unfavorable distribution of crash forces, heightening safety risks. To mitigate this weight increase within the limited space in modern vehicles, designers are increasingly turning to composite materials, which offer an excellent balance of weight, stiffness and strength. These materials provide stiffness comparable to aluminum and density similar to standard injection-molded plastics, making them highly advantageous.
How do lightweight technologies support alternative mobility concepts, and what advantages do polymers and plastic-metal-hybrid solutions have over traditional metal technologies?
Polymers and hybrid solutions are crucial in addressing the weight increase. Although plastic materials may not match metals in mechanical properties, their lower density and greater design freedom often lead to superior component performance within the available design space. Plastics can be shaped with significantly fewer constraints than metals, allowing for better utilization of design space and enhanced overall performance. Hybrid solutions represent the next step in performance, combining the stiffness and strength of metals where necessary with the design flexibility of plastics for functional integration or complex shapes. This approach enables further lightweighting for components that would otherwise need to remain metal.
Where do you see the greatest opportunities and applications for carbon fiber in mass-produced cars, and what are the challenges associated with its end-of-life recycling?
Large, sheet-like components requiring high stiffness and strength against vibrations, and potentially enhanced thermal runaway performance, are ideal for thermoplastic composite materials. Applications include plastic battery enclosures, spare wheel recesses, underbody cladding, front-end modules, control arms and structural reinforcements in the chassis. These thermoplastic composites can be recycled through remelting or shredding for secondary use, unlike epoxy-based composites, which can only be shredded into landfill or incinerated.
What are the new and potential automotive applications for polymers, and how do they contribute to alternative and future mobility concepts?
New automotive applications for plastics are primarily found in components introduced for vehicle electrification. These include e-motor components, busbars, e-axles, and metal replacements for [insulated-gate bipolar transistors], [motor generator units] and inverter housings. Initially introduced in metal due to requirements for thermal conductivity, flame retardance, and EMI shielding, the latest generation of plastics can now meet these needs through modified polymer properties or additional treatments.
When considering alternative materials in vehicle manufacture, what are the key considerations and challenges that need to be addressed?
When adopting alternative material solutions, it is crucial to achieve performance equivalent to traditional materials while improving cost and weight efficiency to maintain a competitive edge. New material requirements, such as thermal conductivity, flame retardance, and EMI shielding, add to the challenge. Additionally, there is increasing pressure to enhance the eco-footprint of materials used in vehicles. Plastics offer multiple benefits in this regard: polymerization requires less energy than aluminum or steel production, conversion into parts (injection molding vs. casting) is more energy-efficient, and lighter components reduce CO2 emissions during the use phase due to lighter designs.
Can you explain how endless fiber reinforced thermoplastic composites can be a cost-efficient alternative to metals in lightweight construction and what advantages they offer?
Continuous fiber thermoplastics offer nearly double the stiffness of aluminum in the fiber direction. Customized tape-laying methods allow for optimal orientation of these materials in the final application, and the ability to overmold in injection molding for complex geometries surpasses the performance of traditional metal parts. This technology enables significant weight and cost reductions compared to metal components requiring extensive machining for precision.