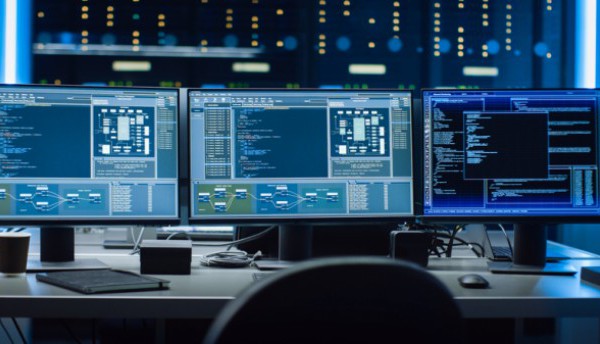
A digital twin (DT) is a virtual replica of a physical asset that uses real-world data and models to improve operations and aid in decision-making. It incorporates real-time and historical data, as well as engineering, simulation, and machine learning models. By creating a digital twin, the automotive industry can gain insights into the performance and behavior of physical assets, optimize operations and make more informed decisions.
The use of DTs in the automotive industry is expected to become more widespread as the digitization of vehicles continues to advance. DTs have the potential to enhance product design, manufacturing processes and vehicle maintenance, resulting in improved products and a more efficient and reliable automotive industry. As this evolution continues, a key priority will be ensuring functional safety and cybersecurity across various automotive processes. By addressing these requirements, the industry can fully leverage the benefits of DTs while maintaining the highest standards of safety and security.
To delve deeper, S&P Global Mobility initiated discussions with leading players in the DT market, including IBM, Ansys, ABB, rFpro, Digiflec and PTC. All are at the forefront of driving architectural shifts and pushing back the technical boundaries. Representatives of each company share their thoughts on the evolving landscape of DTs.
To learn more about how ABB is developing DTs, we spoke to Joerg Reger, managing director of business line automotive at ABB Robotics. ABB is a pioneer of digital innovation in the industry. It is developing a unified digital capability that spans from devices to the edge to the cloud. ABB Ability is its platform that enables seamless interaction between devices, systems, solutions, services, and the platform itself. ABB is also focusing on creating DTs, which require a consistent data model and a communication infrastructure to ensure accurate representation and easy data transfer.
The following is an edited transcript of the conversation.
S&P Global Mobility: What are the most promising automotive use cases for digital twins (DTs)?
Joerg Reger: There is a huge case for digital twins in the design of a vehicle and many manufacturers are already embracing the technology to rapidly accelerate the time to market of cars. Where ABB specializes, and where there is already a great deal of interest and utilization, is in the use of digital twins, such as our leading RobotStudio programming and simulation software, to develop and optimize automotive production facilities. Here the benefits are significant: It allows for faster and more flexible commissioning and production, while also minimizing the chances of errors, and at a lower cost than that of physical trials. The advantages continue long after a production line or plant have been installed too, as digital simulation means adjustments can be made to manufacturing equipment with no disruption to production; new robotic solutions for existing facilities can be quickly evaluated and commissioning times from days to hours. Furthermore, by continuously monitoring (real time) equipment through digital twins, manufacturers can predict when maintenance is needed, reducing downtime and extending the lifespan of machinery. It is also sustainable from the outset, with the simulation helping to minimize energy use and waste without the need for physical trials.
What are the requirements for an OEM to effectively implement DT technology?
For an OEM to effectively use digital twin technology in the development of its manufacturing facilities, all the required data must be available and accurate, including such areas as CAD and textures. A higher initial investment to produce an exact and truly accurate copy of the planned production line in the virtual world is also needed, although this is soon recouped during the commissioning phase and as production ramps up. In some cases, there also needs to be a change of thinking. Production management has traditionally leaned towards hardware tests and investing in dedicated production infrastructure, rather than investing in data quality and data management. While this was once the standard approach it is fast being replaced with effective digital twin software like RobotStudio that requires one investment, compared to hardware tests that require significant investment whenever there is a model change.
What are the primary challenges associated with implementing DT technology?
The biggest challenge is the complexity of transferring an operation from the virtual world into reality. The technology is there but it is far from a straightforward process to replicate in a real-world scenario. The best advice is to start small and then scale up. For example, begin with the digital twin of one production cell and then go from there. In terms of what’s necessary to make the digital twin of a production facility a success, all equipment needs to be built up very accurately in the factory and the robots need to be calibrated in the real world. Tweaks and re-teaching will often be required and inaccuracies in the physical world will need to be compensated for. Vision technology, supported by artificial intelligence, can help the digital twin technology to understand and adjust accordingly for these factors, but it is still a big challenge to just “copy and paste” the programs which have been done virtually in the real world without any changes.
How is the pricing structure for the DT scenario determined? Is it based on the complexity of the scenario, the size of the data or the accuracy of the synthetic data (including the number of sensors used)?
When we look at RobotStudio, our offline programming and simulation tool for robotic applications, the price for the license is per user. The real investment, both in terms of cost and time, is that of the engineers building the digital twins, and that’s common to whatever tool is used to create the digital twin.
What is considered the new standard for vehicle development time, starting from the design freeze phase to production?
While ABB cannot comment on vehicle development time for OEMs, it is seeing manufacturers starting to consider autonomous production during the design phase of a vehicle, so OEMs are certainly considering all avenues in how they can continually work to lower the time from design freeze to production. This is especially so in the transition to EVs, which creates a lot of additional pressure when it comes to establishing production facilities. Digital twins enable virtual prototyping and testing of new products, speeding up the development process and reducing costs associated with physical prototypes. Digital twins enable more effective research and design of products by creating detailed simulations that predict performance outcomes. Normally, developing a prototype of a car takes about three to four years until the design freeze stage, and then 18-24 months to install it. This is usually dependent on whether the plant is a brown field or green field installation.
Is DT technology primarily used in the infotainment and ADAS domains within the automotive industry? Or are there significant advancements expected in other domains like powertrain, chassis and body?
Digital twin technology can be rolled out across all domains. The technology is already widely used in automotive manufacturing and there is huge potential for it to be implemented in all areas of car production, spanning press to body and paint to assembly. However, while many companies are already using digital twins, there are still many that are not, so the effectiveness of the technology on automotive manufacturing is yet to be fully optimized. When it is, it could well be a turning point for the industry in terms of how quickly cars can be built.
How does the sustainability of digital twins compare to traditional physical development in terms of CO2 emissions? What measures are taken to minimize the carbon footprint of digital twin technology?
The environmental benefits of using digital twin software comes through being able to simulate the energy consumption and waste management of production facilities. Being able to digitally simulate changes that will affect these areas, rather than action them in the real world, can provide a much quicker and cleaner insight into their effectiveness. On another level, the logistics of controlling a production facility remotely via a digital twin means a lower carbon footprint due to personnel not having to travel to the manufacturing plant to check or discuss any equipment.
What proportion of the design, testing and validation processes rely on digital twin models compared to physical prototypes?
All three phases can rely heavily on digital twins. Using a digital twin to undertake virtual commissioning of a manufacturing facility and to complete testing of production processes is vital when it comes to quickly ramping-up production lines without risk. The effectiveness of digital twins is long lasting too, with the technology also having significant benefits in the later parts of the life cycle, such as when it comes to maintenance, changes of lines and the introduction of new models into the production line. They help monitoring and maintaining product quality by simulating production conditions and identifying potential issues before they occur. Also, digital twins provide a safe, virtual environment for training employees on new equipment and processes, reducing the risk of accidents and improving overall safety. For supply chain management they offer real-time visibility into supply chain operations, helping manufacturers manage inventory, forecast demand and respond to changes more effectively. In addition, they can help optimize complex processes, such as supply chains, by allowing companies to test multiple scenarios and make data-driven decisions without disrupting real-world operations.
What are the key aspects of digital twins that everyone in the auto industry should be aware of? Also, what cautionary advice would you give to those who are hesitant to embrace digital twins?
Digital twins are essential to the automotive industry, enabling vehicles to come to market in times that, until relatively recently, were considered impossible. Their use is widespread across the industry and this is only going to grow with the transition to electric vehicle production, given the tight timeframes in which they need to be designed and manufactured. It is this scenario which fully illustrates the potential and effectiveness of digital twins — they are an enabler, providing further solutions to help overcome challenges in the fast-evolving automotive industry. Digital twins can provide continuous insights into customer behavior and preferences, enabling companies to tailor their products and services more effectively. For those that are hesitant to utilize digital twins, such an approach will only hinder what is trying to be achieved. To ensure it works, it is vital to start with clean data and focus on the management of this.