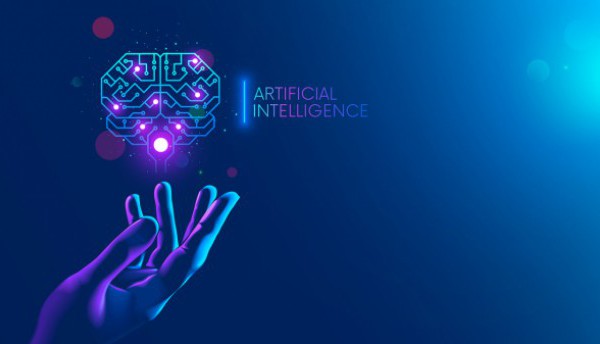
Artificial Intelligence is increasingly being integrated into the automotive industry, primarily to enhance product development through advanced simulation techniques. The shift from physical testing to numerical simulations has led to substantial time and cost savings. However, this transition has created new bottlenecks, particularly with the running times of complex simulations, such as crash tests, computational fluid dynamics and finite element analysis. These simulations can take hours or days to complete, restricting the number of iterations engineers can perform before finalizing designs, which often results in suboptimal performance of components.
AI technologies are being employed to address these challenges by improving the efficiency and speed of simulations. For instance, AI models can provide results comparable to traditional numerical simulations in a fraction of the time, enabling engineers to conduct multiple optimization cycles and explore a wider design space. This capability is crucial for enhancing various performance metrics, including battery efficiency and aerodynamic properties.
Moreover, AI is being used to develop deep physics models that can analyze complex interactions among various physical phenomena, such as flow dynamics, thermal behavior and structural stress. These models allow engineers to visualize results in a manner similar to traditional simulations, thus maintaining the fidelity of the analysis while reducing computational time.
In addition to design optimization, AI contributes to safety improvements in autonomous vehicles by enabling real-time decision-making based on comprehensive modeling of vehicle dynamics. The integration of uncertainty quantification within AI models further enhances reliability by providing engineers with error estimates for their predictions, guiding the refinement of models and ensuring more robust performance in real-world applications.
As the automotive sector looks toward 2025, the continued evolution of AI-driven digital engineering solutions is expected to further streamline complex engineering processes, making them more efficient and accessible across the industry.
To learn more, we spoke to Jacomo Corbo, CEO and co-founder at PhysicsX. UK-based PhysicsX develops AI-driven platforms for engineering workflows, focusing on design optimization and physical behavior prediction. The company serves industries such as automotive, aerospace and renewable energy.
Key takeaways:
- Shift from physical testing to simulation: The automotive industry has transitioned from physical prototype testing to numerical simulations, saving time and costs, but this has introduced new bottlenecks in the form of lengthy simulation runtimes.
- Acceleration through AI: Advanced AI platforms using geometric deep learning can dramatically reduce the time required for complex simulations from days to seconds, enabling more iterations and optimizations in the design process, ultimately improving performance and efficiency.
- Enhanced simulation fidelity: Deep physics models (DPMs) offer high fidelity in simulations by incorporating comprehensive 3D data, allowing engineers to analyze complex interactions among various physical factors, thus improving understanding and decision-making.
- Lifecycle efficiency and knowledge retention: AI-driven models capture and retain institutional knowledge throughout the engineering lifecycle, allowing for continuous improvement and application across design, manufacturing and operational phases, which enhances overall efficiency and innovation in the automotive sector.
The following is an edited transcript of the conversation.
S&P Global Mobility: Can you elaborate on how your AI platform addresses bottlenecks in automotive product development and the types of simulations it creates to enhance the design process for engineers?
Jacomo Corbo: Large amounts of money and time have been saved in the automotive sector by steadily moving more and more validation work to numerical simulation tools rather than the physical testing of prototype parts and vehicles. However, this has pushed the bottleneck elsewhere.
It is now the running time of the highly complex crash simulations, computational fluid dynamics simulations, and finite element analysis structural simulations themselves that are slowing down development. The most complex of these can have running times of multiple days. And even simulations of individual components in isolation can have running times of several hours.
This means that for many systems, the development plan only allows for two iterations through simulation before the project must move on. As a result, performance gains are being left on the table and parts are often far from optimized at the point they are sent for manufacturing.
Our AI platform, based on geometric deep learning, provides the equivalent fidelity and accuracy of results that you would get from traditional numerical simulation but in seconds rather than hours or days. This means the time savings can either be banked and the time to market for the project shortened. Or the time saving can be used to run component and system optimization loops across a very wide design space of possibilities. This can unlock the battery efficiency, aerodynamic performance and drivetrain power density required to push the sector forward.
How does your platform differentiate itself from other AI solutions in the automotive industry, particularly in terms of simulation capabilities and the specific benefits it offers to manufacturers?
There are many approaches to AI that can be beneficial to the automotive industry. But the foundation models, model architectures and tooling on our platform are all specifically tailored to one specific approach — the development of geometric deep physics models (DPMs). We think these models are the best for tackling some of the toughest problems in the automotive industry.
Rather than the classic approach of using AI to map parameters (such as width and height) straight to outcomes (such as the coefficient of drag), DPMs learn based on the entire mesh of 3D data that sits in between. This means that they can infer an element of the underlying physics of the problem, and it also makes them highly data-efficient because each node of the mesh is a unique data point that the model can train on.
This allows models to handle situations where multiple types of physics (such as flow, temperature and stress) are at play simultaneously. It also allows the engineer to view the model results as a complete stress field or flow field, in the same way they are used to with traditional simulation. This allows them to better understand the nuances of the problem.
In what ways does your platform support the development of autonomous vehicles, especially regarding simulation accuracy for real-time applications?
This is a great strength of the models that we build. Typically, applications that require real-time control have to use highly simplified approximations of reality in order to be fast enough to use in real time. Using deep physics models (DPMs) within control systems can give the best of both worlds. They are fast enough to respond in real time; however, the response you get is based on full fidelity modeling of the true underlying physics of the problem. An example might be a battery controller for an electric vehicle. Using a DPM within the control loop would allow the response to be based on a model that contains predictions of the coolant flows and the true electro-chemistry of the battery rather than simplified approximations.
Could you explain the role of uncertainty quantification in your models and how this feature helps build trust in AI-driven engineering within the automotive sector?
Uncertainty quantification (UQ) is critical in several phases of an AI-driven engineering workflow. At its simplest, receiving an uncertainty quantification with every prediction allows the engineer to get a sense of the error bars inherent in their work. Traditional numerical simulations are also approximations of reality, but UQ is often less emphasized in these tools.
On top of this, UQ can also be a critical tool to help guide the development of a deep physics model. Often the areas within the design space that show the highest performance are close to the edge or even outside of the original training data for the model. As a result, the uncertainty will be at its highest. However, this signal can be a useful trigger for adding more training data to the dataset specifically in the areas of highest performance, thereby reducing uncertainty. In sophisticated applications, this active learning loop can be automated.
How can AI enhance the efficiency of automotive design and manufacturing processes, and in what ways can it be used to improve safety features in vehicles, particularly for autonomous driving?
Often the results from numerical simulations are archived or thrown away after whatever decision they were contributing towards has been taken. As a result, this traditional approach to automotive development duplicates a lot of effort and results in a loss of institutional knowledge with each iteration.
In contrast, the development of AI models to solve engineering problems captures and reuses institutional knowledge with each new project. The models continue to get more powerful and more flexible over time as more training data is added.
Additional efficiency comes from the fact that a single model can be used across design, manufacture and operation. For example, a model that helps with the design of a battery pack can also be used in manufacturing to understand the impact of certain defects on performance. Components can be rejected or accepted accordingly based on their true performance. Finally, that same model can be used in the operation of the battery pack as part of its thermal management system. So a single model is applicable across the entire engineering lifecycle.
How do you see your sector developing in 2025?
We expect a new class of AI-first digital engineering solutions to be a major growth opportunity in 2025. These AI models will dramatically accelerate accurate physics simulation, enable generative engineering, and accelerate some of the most time-consuming activities in the engineering process, making complex engineering across industries more accessible.
Engineering design processes were transformed by numerical simulation and the availability of high-performance compute infrastructure. The move from numerical simulation to deep learning represents a similar leap.