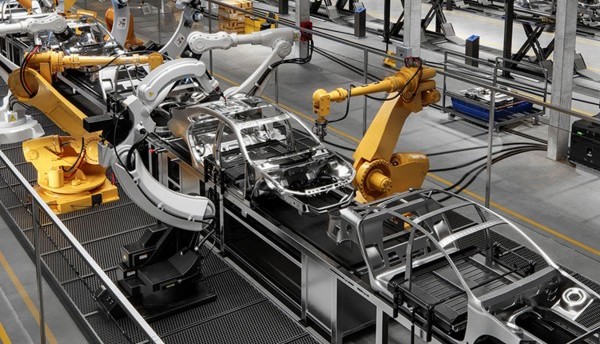
Gigacasting is a hot topic in the automotive industry right now. We continually receive calls from clients on the subject, either concerned about how it’ll change their market prospects or warning of the perils of this ‘eggs-in-one-basket’ strategy.
They’re right about the perils. It’s a long list. Massive castings can cost up to 10 times more than what they’re replacing. They may have distortion issues, may remove important repair capabilities. What’s more they require intensive end-of-line inspection scanning. Oh, and they all come after the ordering of a custom-built gargantuan piece of tooling, moving it into place and figuring out how to efficiently work the temperamental processes.
We’ve covered the above issues many times on AutoTechInsight, but still the questions come. Why are established industry suppliers worried about big dreams with massive headwinds? Do casting experts have enough technical solutions to known operational problems? Can ADAS systems prevent enough crashes to make up for unrepairable castings?
Simple answer: it's not about the components, or gigacasting per se, it’s about the assembly plant. If you've made it this far, maybe you understood the tongue-in-cheek theatre reference in my title. The metaphor paints a useful framework for what is really happening here.
Initial concerns from many players are about market share of advanced steels, stampers of those components, and conversion rates in adoption scenarios. By my estimates 15-20% of body-in-white (BIW) stampings in 2030 may be at risk. Underbody components typically comprise about 50% of a vehicle's BIW shell, and this soft belly is the target of gigacasting's attack.
The real story isn’t about the material and methodology change to the underbelly of light vehicles, but the creative processes themselves which are under transformation. Expertise within suppliers, factory designs and vehicle configurations are all changing. We are approaching a disruption to the auto industry's backbone: the assembly line.
While robotics, automation, industry 4.0 and blockchain all have impacts to the efficiency, cadence and support networks of modern assembly plants; the overall assembly line process stood for 110 years as the uncontested champion of high-volume manufacturing. Components may be sub-assembled offline, lasers might scan each part for dimensional accuracy, and a bolt might even hold all the measurement data from rigorous testing of a powertrain - but the assembly line itself evolved to absorb these improvements. No revolution to assembly efficiency stood to threaten the linear model until now.
OEMs are looking towards gigacasting not as a component, but as a change to how their entire world functions. Kind of like introducing computer-generated graphics into an industry which relied upon staging, crews and well-rehearsed scripts. Single-piece front and rear castings may not be the penultimate design of automotive evolution.
However, the reconfiguration of the dance played behind factory walls will forever change economies within automotive. Whether corner castings or single-piece, whether gigacast or gigapress, a change to how vehicles come together is upon the industry. Nodal construction will replace linear, bottlenecks will arise and dissolve, and something altogether new will be born.
Suppliers and OEMs should take this all into consideration when evaluating the strategic horizon aligned with these casting questions. It's not about the exact material and implementation, but it is all about how an entirely new workflow can be enabled for improved productivity. When OEMs successfully create their new dances for factory floors, an automotive renaissance will begin.