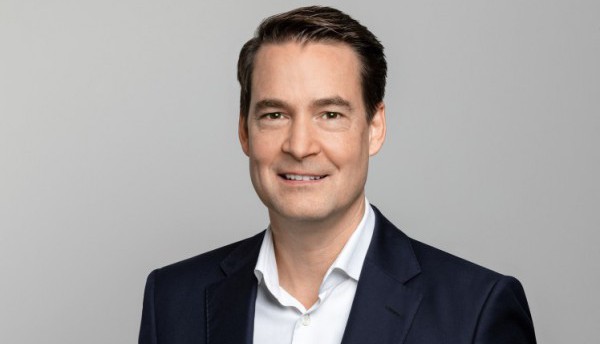
Global supplier of automotive components ZF Friedrichshafen AG has developed a scalable and modular e-motor inverter architecture that can offer electric vehicle (EV) makers maximum flexibility from 400V to 800V, from silicon to silicon carbide, the company had announced on 4 January 2022. The company said that its innovative inverter combines advanced inverter design, next-generation power semiconductors, and highly intelligent software algorithms, leveraging its expertise in developing the electric drives aimed at enhancing efficiency and power output and shorten development cycles.
“The combination of greater scalability and modularity with increased efficiency, peak power, and affordability of e-motors is the key to success within the e-mobility market. The inverter is also where development cycles from the software industry and semiconductor innovations meet automotive hardware and integration expertise. This is where future differentiation will happen,” said Stephan von Schuckmann, member of the ZF board of management. Notably, Schuckmann is also responsible for ZF’s electrified powertrain technology division.
According to the company, the innovative modular inverter platform is not dependent on predefined semiconductors and is designed to support vehicle manufacturers in bridging the silicon–to–silicon carbide transition while also being prepared for future semiconductor trends.
ZF said that its new inverter systems are being readied for next-generation e-drives that are expected to go into production by 2025.
Significance: It is understood that the inverters work as the brain of electric drivetrains, managing the flow of energy from the battery to the e-motor, and vice versa. Over years, as powertrain technology evolves to suit the needs of electric mobility applications, inverters have become more efficient and more complex in every development stage. ZF said that the next evolution in this component would be in the combination of the inverter design, next-generation power semiconductors, and highly intelligent software algorithms.
On the semiconductor and software side, ZF said the company has been working toward the transition to alternative powertrain technologies over years and that it has developed a deep expertise and knowledge on the inner workings of e-drives, from the holistic design of these systems to software optimization linked to new power semiconductors.
The efficiency and peak power of an inverter is not only defined by the properties of the power semiconductors, but also significantly defined by software, the company said, adding that the inverter technology and control software alignment are critical and can be achieved by feedback loops, wherein the inverter hardware provides the software a flow of information pertaining to current, temperature, and DC-link voltage, among others. This information is used to optimize pulse patterns and switching strategies in real time to improve efficiency and peak power.
“Especially for silicon carbide–based systems, ZF has found a solution optimizing the link between the power semiconductor boundary conditions and control software in order to gain the full potential from the semiconductor configuration,” the company said in its note.
ZF further added that its new inverter generation brings hardware and software optimization functionalities to its customers to realize faster power semiconductor switching times, better short circuit protection, and other benefits.
“As the industry moves rapidly toward an electrified future and the goals of zero emissions to enhance our environmental future, ZF has the expertise and owns proprietary software and gate drive functions to accelerate the transformation. From significantly faster and safer short circuit protection to gate drivers realizing the absolute maximum performance of power semiconductors, ZF is well-positioned to fulfill the needs of the industry and society,” said Schuckmann.