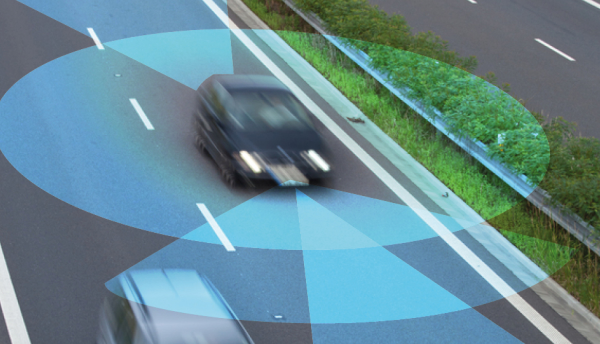
The automotive industry is starting to take an interest to a new form of manufacturing, called Additive Manufacturing (AM), more commonly known as 3D printing. 3D printing uses built-up layers of deposited materials to build a component. Successive layers of a material are stacked up one over the other until the component is formed.
While companies have been experimenting with AM for some time, last week Mercedes-Benz Trucks announced the development of its first spare part made of metal using 3D printing technology. The part was a thermostat cover for truck and Unimog models from older Mercedes-Benz model series, the first time the company has made available a 3D printed spare part . The company has claimed that the component has a is of a similar quality compared to the original part.
Mercedes-Benz Trucks has been supplying 3D printed plastic spare parts since September 2016. In an e-mail response to IHS Markit, Mercedes-Benz Truck spokesperson informed that Daimler in fact has been working with the 3D printing technology for more than 25 years. But with the development of metal 3D printing, the scope for the technology has increased significantly. The use of metal allows for manufacturing of parts which are of similar quality to the conventionally manufactured parts.
3D printing in automotive today
We have already seen a few automakers and technology suppliers build parts using 3D printing. Japanese automaker Honda showcased a 3D-printed electric vehicle (EV) concept during the Combined Exhibition of Advanced Technologies (CEATEC) trade show in October last year. Called the Micro Commuter, the concept has been produced in co-operation with Japanese tech firm Kabuku. Instead of featuring traditional body panels, the vehicle's bodywork was entirely 3D printed.
Earlier this year, Audi, formed a new development partnership with Germany-based EOS e-Manufacturing Solutions to develop metal-based AM systems and processes. Audi has set up its own competence centre for 3D printing in order to gain experience with the materials and the process. The company said that Audi aims to revolutionize the process of tool manufacturing. “The company plans to further develop the materials for series production. With AM technology, Audi plans to integrate internal structures and functions in tools that they have not been able to create so far with conventional manufacturing methods,” Audi had said.
US automaker Ford is also experimenting with 3D printing technology to manufacture large one-piece auto parts. The company is looking to build components such as spoilers for its future prototypes and production vehicles.
3D printing at the moment is primarily used for quick prototyping and small-scale pilot programs. However, a gradual increase in its usage is already visible. In November 2016, Germany-based GKN Sinter Metal started mass-scale 3D printing of precision parts for engines and transmissions at its plant in Radevormwald, Germany. The company installed a new additive manufacturing machine called the ‘MetalFAB1’, which it claimed was the first ever deployment of the machine in the automotive industry. GKN said last November that it would use the MetalFAB1 machine, manufactured by the Dutch company Additive Industries, to produce small and medium-sized series of complex automotive components for the original equipment and replacement parts markets.
Currently, 3D printing is used for making mainly exterior and interior components such as bumpers, fenders, body panels, seating, dashboards and even tires and wheels, albeit at a relatively small scale. With new materials now becoming viable for 3D-printing, even powertrain and drivetrain components are being manufactured, which can withstand high temperatures, as well as chassis and suspension parts that can sustain extreme strain for long durations.
Advantages of 3D printing
3D printing allows a digital file to be converted directly into a 3-dimensional object, typically by laying down many thin layers of a material in succession. The digital design file is sent to a 3D printer which then analyzes the design and physically prints it, layer-by-layer. This allows for extremely quick design validation and prototype development. In just a matter of hours, a component can be brought from design stage to production stage.
Not only does it save time, it also leads to significant cost reductions in more ways than one. Through 3D printing, companies can completely eliminate wastage of raw materials, as 3D printing uses the exact amount of material required. This also makes this form of manufacturing suited for making lighter components. In an interview published on GKN Sinter Metal's website in March, Additive Industries CEO Daan Kersten said, "GKN and AI are now beginning to focus on how to optimize the use of GKN powders and explore the possibilities of using water-atomized powders. In terms of our integrated AM series production system, total cost per part is crucial, so we continue looking at lowering these costs for 3D printed parts by eliminating labor, reducing the system costs and increasing productivity. Together with GKN, we are working on reducing the material costs as well.”
The technology also works with complex designs and structures that are otherwise challenging to produce in conventional manufacturing. Although plastic has been the most widely used material for this form of manufacturing, it has been shown that various other kinds of material and metals can be used for 3D printing, expanding the number and types of components that can be produced.
What 3D printing holds for automotive industry
With the growth of electro-mobility and autonomous driving, the automotive industry has becaome an area of interest for technology companies and number of start-ups that have with almost zero experience in manufacturing. 3D printing could prove to be valuable tool to such companies in bringing down the entry barrier into the industry and compete with established automakers.
For automakers, 3D printing provides an opportunity to modify their supply chains to make them more efficient, as it provides the option of on-location and on-demand production of components. Mercedes-Benz Trucks has already started thinking in this direction. “In the future, 3D metal printing might allow decentralised and therefore, much faster, local production directly in Mercedes-Benz production locations worldwide. This would further improve parts availability and make expensive warehousing and the associated, complex transport processes unnecessary, with delivery times made shorter for customers,” said a company spokesperson.
While the possibilities of 3D printing are visible on the horizon, there are still a number of issues that before this manufacturing technology can be used for mass-production of components for vehicles. What is an advantage during prototyping, quickly turns into a major disadvantage when it comes to series-production. One component can take many hours or even days, depending on the size of the component, to be fully built and processed to be ready for use. The limited installation space in the "printer" limits the number of components that can be produced per system. This amount of time is unviable for the automaker that has to churn out hundreds of cars in a day. “In the automotive industry the requirements are high in terms of productivity, reliability and predictability. Together with GKN, we continue to drive improvement of both performance and cost levels. We really want to work on system development for larger volumes, and as a major player in the automotive supply chain, GKN’s know-how in automotive production is practically unrivalled, as they produce 11 million car parts per day. Because they are so intimately familiar with high volume production, they are the ideal partner to help us test our system in light of those stringent automotive requirements,” Additive Industries’ Kersten said in the interview.
Analyst: Srikant Jayanthan