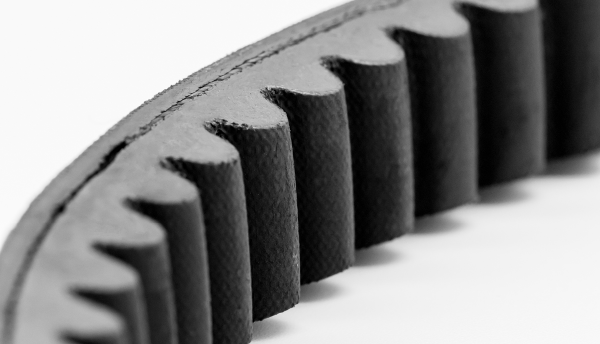
The large earthquakes that occurred on 14 and 16 April affecting the southern Japanese city of Kumamoto have disrupted the domestic automotive industry and caused production interruptions at a number of component and OEM manufacturers based in the affected region, with Toyota worst hit. According to official announcements and IHS Automotive research, we expect the situation at suppliers Aisin Seiki and Renesas to be key to how quickly normal operations resume in the industry.
Aisin Seiki produces body and engine components and has three factories in Kumamoto Prefecture; two of these have halted operations because of the aftershocks, and these stoppages mainly affect production at the Toyota Group. The resumption plan is still to be determined, but Aisin is aggressively trying to resume operations and is looking at alternative sourcing from its other plants.
Renesas meanwhile has its Kawajiri plant in Kumamoto city and operations there have stopped since the earthquake hit on 14 April. Semiconductors used in Toyota engine control units (ECUs) are the key product. Renesas will announce a recovery plan tomorrow (21 April).
Toyota most affected
The impact on the supply chain in the Kyushu area is forcing temporary production stoppages at Toyota, Nissan and Mitsubishi. Toyota Group is most affected and it could take more than four months for the company to recover all of its lost volumes. Toyota announced today (20 April) that it expected to resume production at 18 affected assembly lines between 25 and 28 April.
Mitsubishi meanwhile halted operations at its Mizushima plant from 18 April (night) and 19 April. Nissan resumed operations at its two Kyushu plants from 18 April, although IHS Automotive forecasting analyst Satomi Hamada says that a parts shortage could temporarily hold up production. The impact on Nissan and Mitsubishi will not be as great as it is for Toyota as they are less reliant on supplies from Aisin Seiki and Renesas in the Kumamoto area, and they are expected to recover any losses within one month.
Toyota's domestic assembly lines are being suspended for the second time this year. In February, the automaker halted work at its factories from 8 to 13 February following an explosion at a steel plant operated by its affiliate Aichi Steel. According to IHS Automotive global production forecasts, Toyota (excluding joint-ventures) carries out 39% of its vehicle production in Japan, making the country its single most important vehicle assembly source. North America is its second largest production location, with 19.5% of total output.
Most of the automakers in Japan follow a just-in-time/sequence process for deliveries of components, systems and modules. Under this system, automakers receive parts according to their production schedules, saving them from building up inventory. After the devastating earthquake and subsequent tsunami in 2011, however, Japanese automakers took steps to make the process more resilient to natural disasters, such as by maintaining supply-chain databases. However, last week's earthquakes have affected suppliers' facilities, disrupting the supply chain. Until suppliers resume deliveries, automakers cannot restart assembly operations. Yet suppliers' ability to resume production depends on several factors, including how severely the earthquakes damaged not only their plants but also those of their tier two or raw material suppliers.
*Light vehicles only (GVW >6T)
Outlook and implications
The situation remains in flux, so IHS is considering two scenarios: a base scenario and a pessimistic scenario. In the base scenario, we assume that the recovery plans at Aisin Seiki and Renesas support the resumption of vehicle plant operations in the week beginning 25 April. In this scenario, the net loss would be equivalent to 2.1 days in April, which equates to 70,000 units, of which 66,000 units would be lost by Toyota Group across 15 plants. Toyota would need to add approximately three additional working days until June to recover the lost volumes under this scenario.
In the pessimistic scenario, we see the impact on the supply chain running deeper and affecting Toyota plants until the end of the month. In this scenario the net loss could rise to 127,000 units for the group and Toyota would need to operate additional working days through to August to recover. Even in the pessimistic scenario, we expect supply restrictions to be cleared by the third quarter of 2016, enabling domestic sales to grow comfortably in the fourth quarter of 2016 before the consumption tax increase in the first quarter of 2017. Fortunately, there has been no tsunami following these latest earthquakes, so replacement of damaged vehicles will have less of an impact compared with the 2011 earthquake.